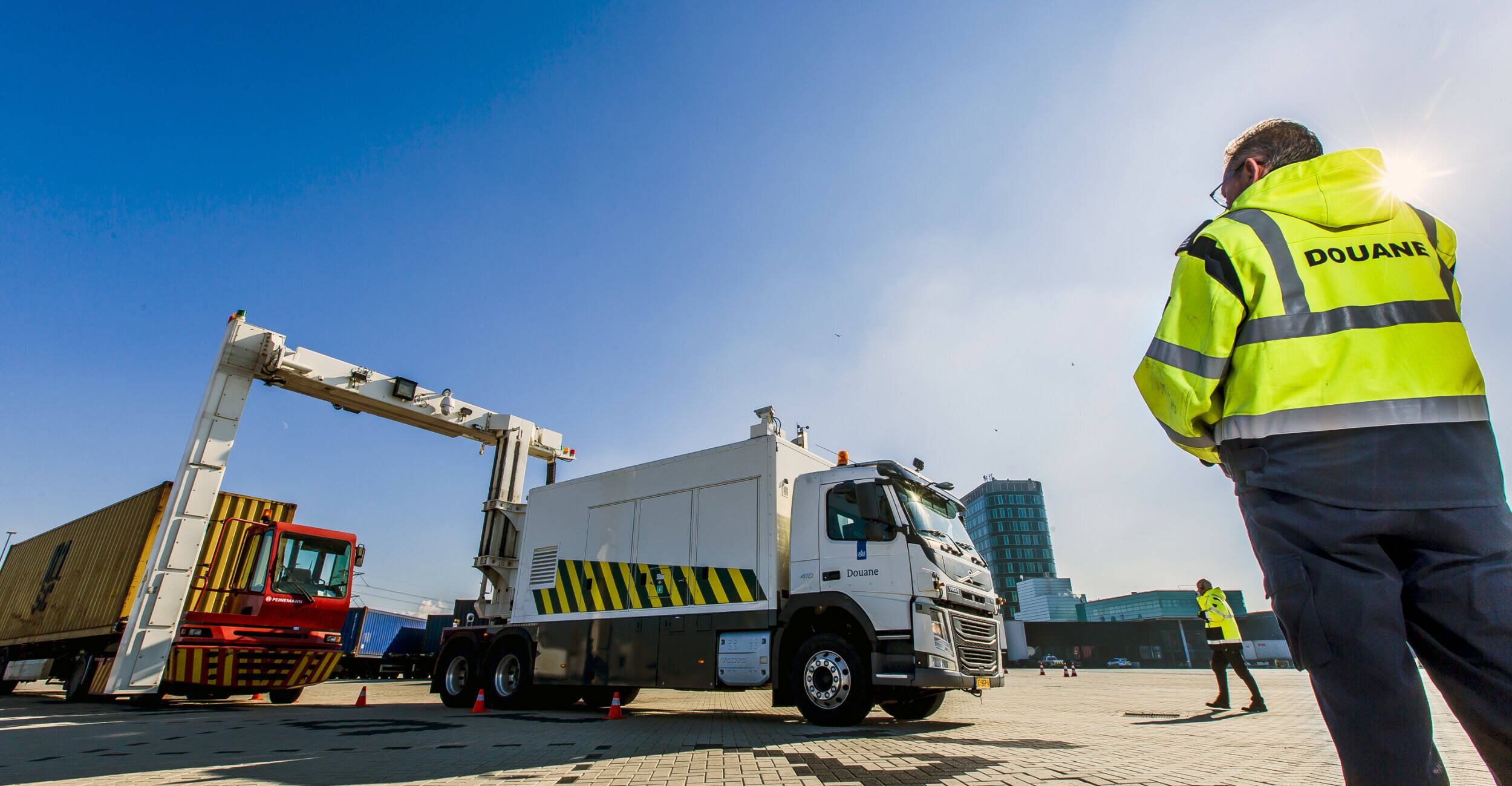
Successful digitalisation of customs processes
High-tech Customs Scan
All large container terminals on Rotterdam’s Maasvlakte now have a high-tech Customs scanner on-site. Customs analyses images of containers’ contents remotely, 24/7. Therefore, containers no longer have to be moved off-site or opened up unnecessarily, and 95% are cleared within 36 hours of offloading. “This is one of the first quantifiable outcomes of our collective efforts,” stated Customs.
TURNAROUND TIME
REDUCED BY 30%
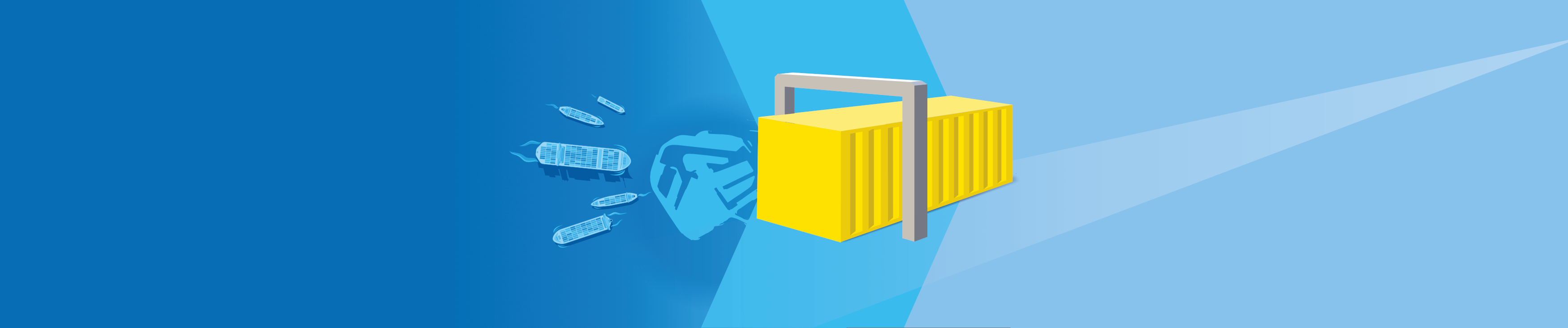
More to come
The parties will naturally continue with this data-driven approach, and view various processes in Rotterdam through a critical lens. A next step can be to give priority to reefer checks throughout the chain. To be continued.
Customs Dashboard
It has even become possible to share forecasts, extrapolated from historic data. Also, problem areas can be better substantiated, for instance through digital tools like the Customs Dashboard, which has been operational since the start of this year and shows the shorter turnaround times. “This dashboard is the result of a data-driven collaboration between Customs and the Port of Rotterdam Authority, through which information is exchanged, analysed, and translated into business value. This is very important step, because only when something has business value can you set a course for it,” adds the Port of Rotterdam Authority.
At least as important is that, thanks to improved collaboration and further digitalisation of processes, more data are available. Data that will be used to provide more insight. Currently, it is possible to pinpoint where in the chain a container is held up – and why. Also, the exchange of data is much improved. This way, it’s possible to flag problem areas at an early stage and respond proactively.
Communication and security crucial
Aside from economic value and sustainability, the security of reefer containers from South America has become a growing issue over the past few years as well. Logistics processes are being disrupted as a result of drug trafficking and crime-related issues. Digitalisation of customs processes helps minimise wait times and increases chain efficiency and security. Portbase’s Port Community System (PCS) enables efficient and straightforward coordination and exchange of information in Rotterdam. This helps prevent data fraud and makes it harder to illegally pick up containers with drugs. Also, it’s important to realise that this is a matter of collaboration between Customs, ship agents, terminals, shipping companies, carriers, and other stakeholders in the chain. Communication between these parties is a key factor in determining the efficiency and security of the entire checking process. This is crucial, especially for reefer containers with their perishable contents.
Of course it’s a matter of economic value but more is at stake, according to GroentenFruit Huis, which advocates for the interests of companies in the fruit and vegetables business. “Especially in light of the increase in sustainability awareness, we see a growing focus on avoiding food wastage. Nobody wants to throw out food anymore. Therefore, in recent years, the need for faster inspections, minimal waiting times, and fewer disruptions increased. In addition, regulations for growing fruit and vegetables are only getting stricter. Fewer pesticides are allowed, which only made these products more vulnerable.
Avoiding
food
wastage
“Previously, customs checks were entered manually and communicated via, for instance, email. If a check notification was entered on Friday night, it was sometimes only picked up on Monday morning. This, of course, meant that a container would be sitting for three days. Now, notifications appear on the schedule instantly, with shorter waiting times and processes as a result.
Logically, cargo owners and end users benefit the most from this increased digitalisation. Shippers report that turnaround times in the inspection process are markedly shorter. “Almost all excesses, such as containers sitting for more than five days, have been eliminated from the system. We see a reduction of processing time of more than 30%, especially thanks to the reduction of these excesses. And our goal is to reach as much as 50% next year. In addition, Customs sees a significant reduction in the number of complaints, up to 80%. And complaints, at the end of the day, also take time to process.
Since 2020, the Port of Rotterdam Authority, Customs, Fresh Produce Center and Portbase are working on further digitalisation of customs processes to facilitate more efficient and safer checking of containers. The desired result being: the reduction of turnaround time. Read all about the steps that have been taken since and the lessons learned.
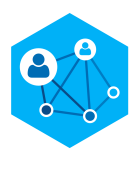
Case study 1
Scroll down
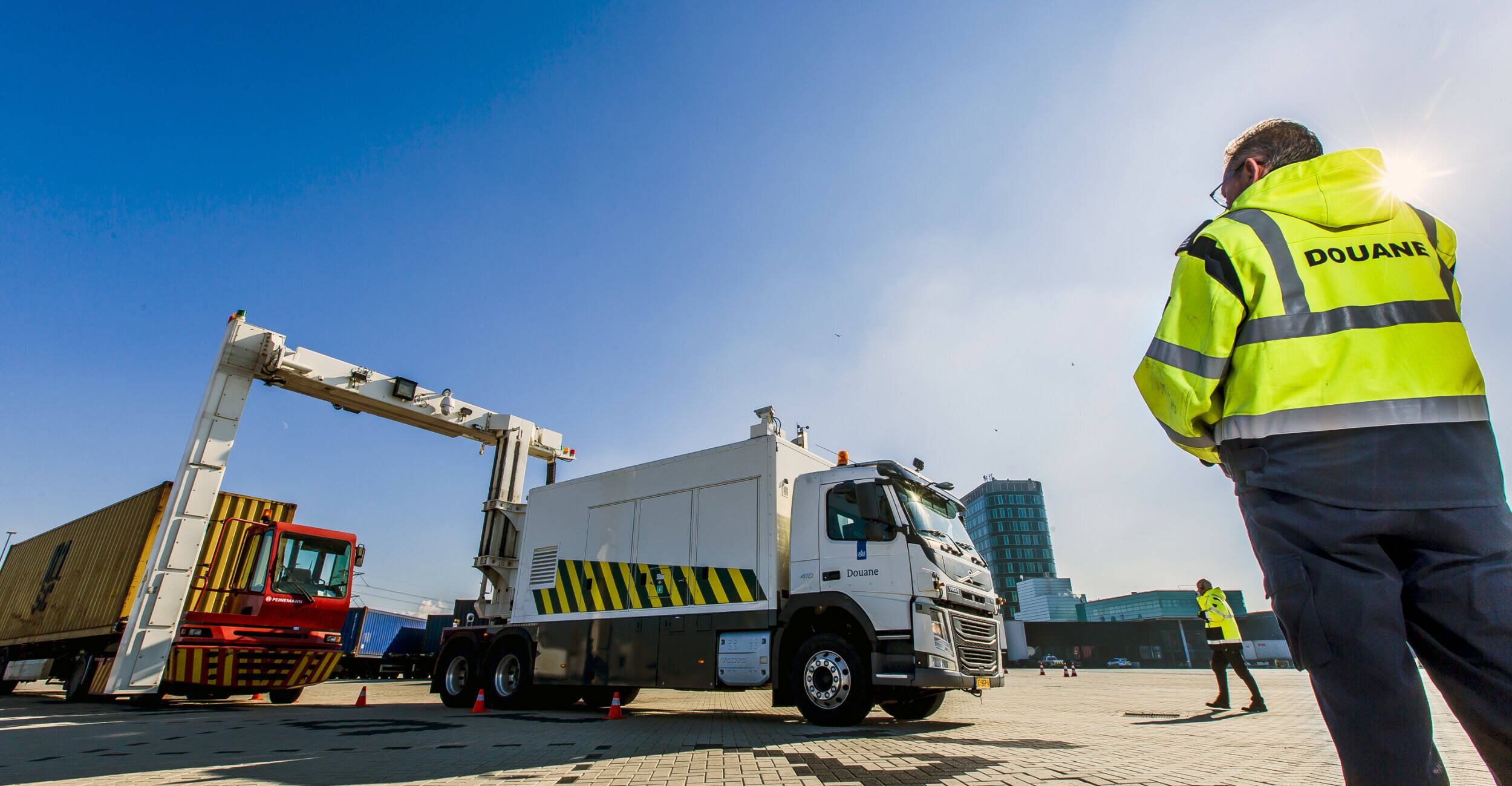
Successful digitalisation of customs processes
High-tech Customs Scan
All large container terminals on Rotterdam’s Maasvlakte now have a high-tech Customs scanner on-site. Customs analyses images of containers’ contents remotely, 24/7. Therefore, containers no longer have to be moved off-site or opened up unnecessarily, and 95% are cleared within 36 hours of offloading. “This is one of the first quantifiable outcomes of our collective efforts,” stated Customs.
Avoiding food
wastage
Of course it’s a matter of economic value but more is at stake, according to GroentenFruit Huis, which advocates for the interests of companies in the fruit and vegetables business. “Especially in light of the increase in sustainability awareness, we see a growing focus on avoiding food wastage. Nobody wants to throw out food anymore. Therefore, in recent years, the need for faster inspections, minimal waiting times, and fewer disruptions increased. In addition, regulations for growing fruit and vegetables are only getting stricter. Fewer pesticides are allowed, which only made these products more vulnerable.
“Previously, customs checks were entered manually and communicated via, for instance, email. If a check notification was entered on Friday night, it was sometimes only picked up on Monday morning. This, of course, meant that a container would be sitting for three days. Now, notifications appear on the schedule instantly, with shorter waiting times and processes as a result.
The parties will naturally continue with this data-driven approach, and view various processes in Rotterdam through a critical lens. A next step can be to give priority to reefer checks throughout the chain. To be continued.
More to come
It has even become possible to share forecasts, extrapolated from historic data. Also, problem areas can be better substantiated, for instance through digital tools like the Customs Dashboard, which has been operational since the start of this year and shows the shorter turnaround times. “This dashboard is the result of a data-driven collaboration between Customs and the Port of Rotterdam Authority, through which information is exchanged, analysed, and translated into business value. This is very important step, because only when something has business value can you set a course for it,” adds the Port of Rotterdam Authority.
At least as important is that, thanks to improved collaboration and further digitalisation of processes, more data are available. Data that will be used to provide more insight. Currently, it is possible to pinpoint where in the chain a container is held up – and why. Also, the exchange of data is much improved. This way, it’s possible to flag problem areas at an early stage and respond proactively.
Customs Dashboard
Aside from economic value and sustainability, the security of reefer containers from South America has become a growing issue over the past few years as well. Logistics processes are being disrupted as a result of drug trafficking and crime-related issues. Digitalisation of customs processes helps minimise wait times and increases chain efficiency and security. Portbase’s Port Community System (PCS) enables efficient and straightforward coordination and exchange of information in Rotterdam. This helps prevent data fraud and makes it harder to illegally pick up containers with drugs. Also, it’s important to realise that this is a matter of collaboration between Customs, ship agents, terminals, shipping companies, carriers, and other stakeholders in the chain. Communication between these parties is a key factor in determining the efficiency and security of the entire checking process. This is crucial, especially for reefer containers with their perishable contents.
Communication and security crucial
Logically, cargo owners and end users benefit the most from this increased digitalisation. Shippers report that turnaround times in the inspection process are markedly shorter. “Almost all excesses, such as containers sitting for more than five days, have been eliminated from the system. We see a reduction of processing time of more than 30%, especially thanks to the reduction of these excesses. And our goal is to reach as much as 50% next year. In addition, Customs sees a significant reduction in the number of complaints, up to 80%. And complaints, at the end of the day, also take time to process.
TURNAROUND TIME
REDUCED BY 30%
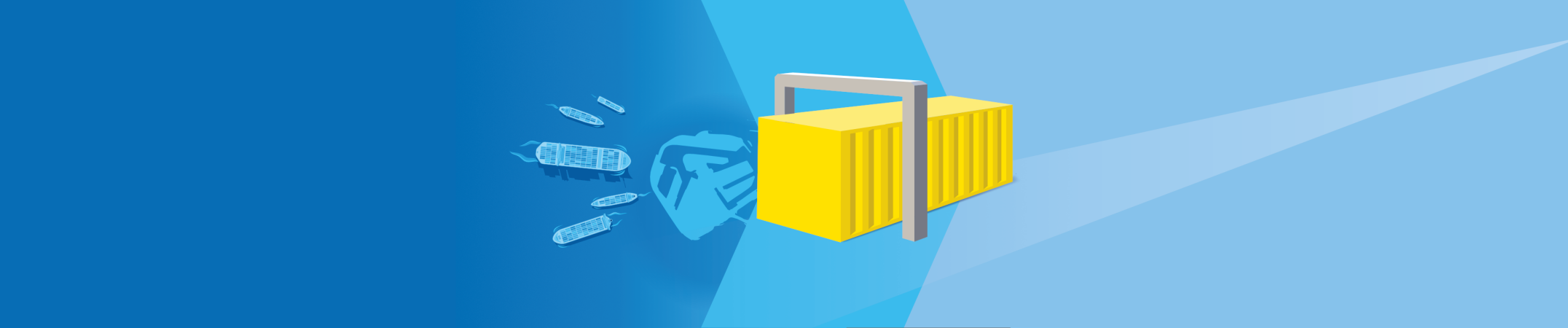
Since 2020, the Port of Rotterdam Authority, Customs, Fresh Produce Center and Portbase are working on further digitalisation of customs processes to facilitate more efficient and safer checking of containers. The desired result being: the reduction of turnaround time. Read all about the steps that have been taken since and the lessons learned.
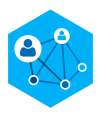
Case study 1